Clarebout
French fries should be called Belgian fries. Together with beer and chocolate, they are Belgium’s national pride. And they know it abroad too. Belgian producers of frozen French fries can present excellent growth figures, thanks in part to exports. Family business Clarebout Potatoes has become one of the most important players in that market with a focus on the highest possible quality and food safety. To keep up with demand, it invested in a new site in Dunkirk. Indinox supplied and installed all the utility lines for compressed air, water and oil.
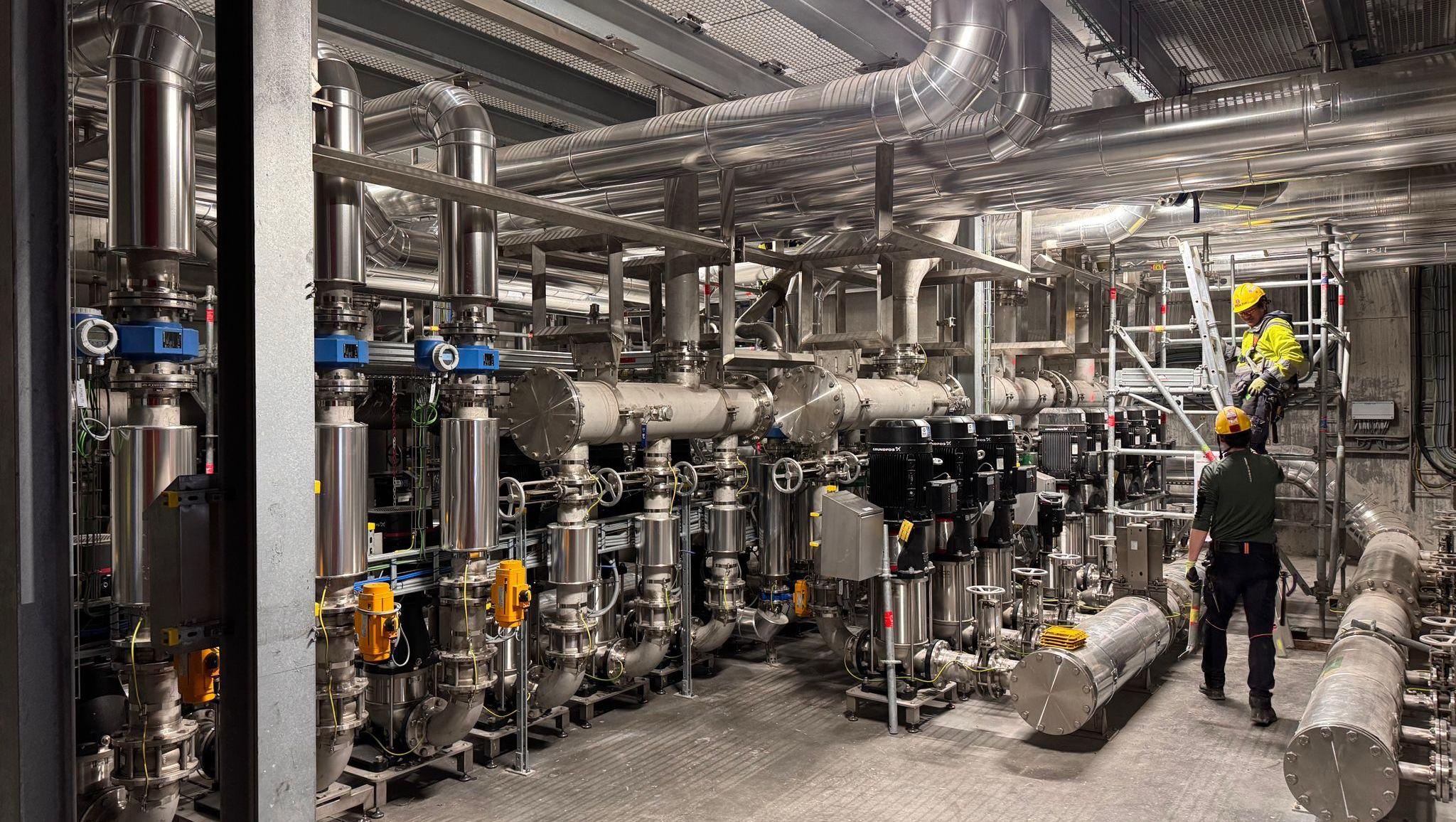
“Clarebout sets the bar very high in terms of quality, and so do we.”
SERVICES
First foreign investment
In the space of 35 years, founder Jan Clarebout has turned Clarebout Potatoes into a global player. A story that is far from over. Over the past three years, sales have doubled. Clarebout Potatoes therefore had to look for a way to expand its capacity and found just the right place across the border in Dunkirk. This was the company's only first foreign investment, as it wants to keep its knowledge close to home and not move to America or Asia. The existing branches are also located a stone's throw from the French border, in Nieuwkerke and Waasten.
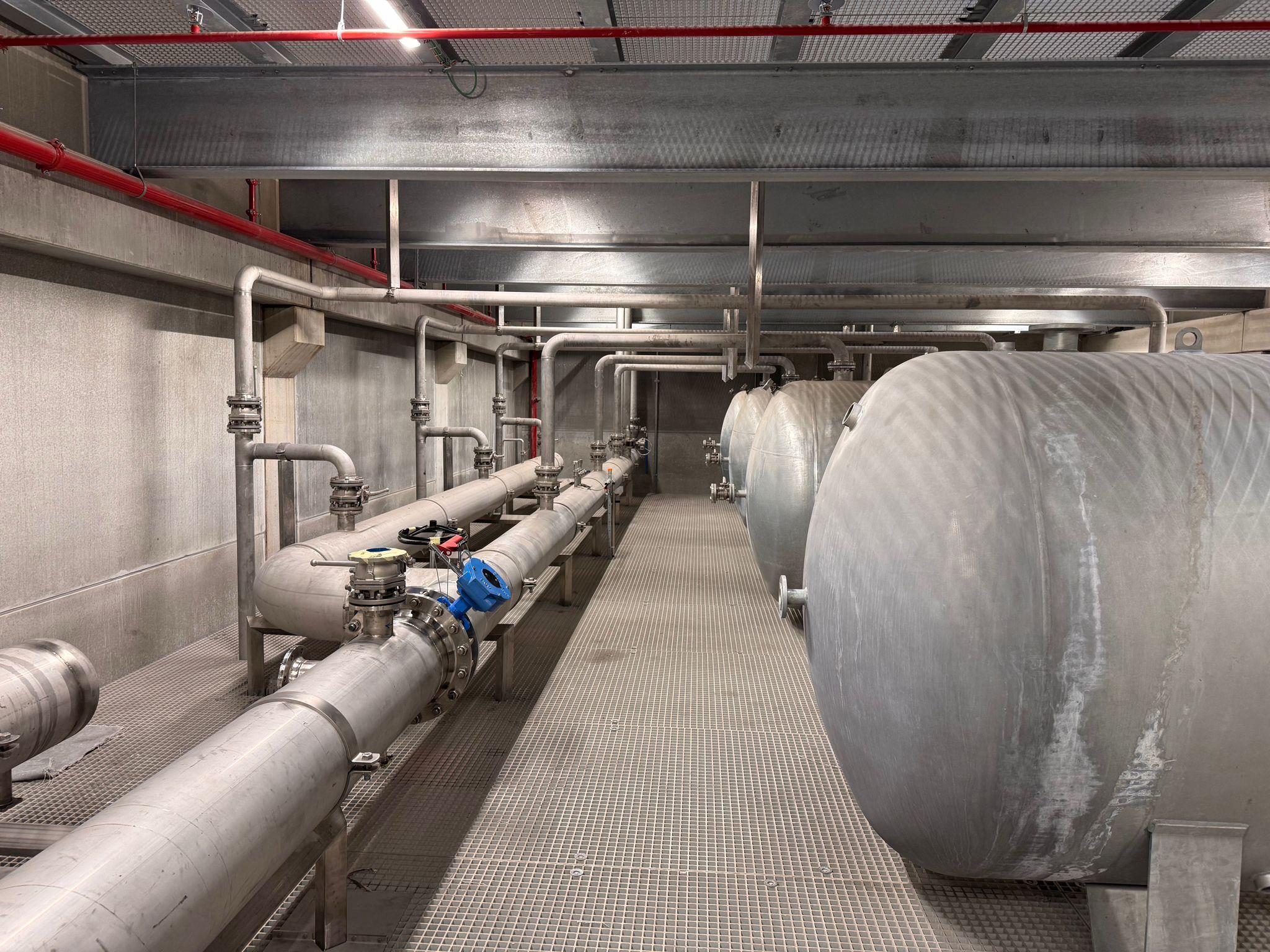
320 tons of potatoes per hour
In Dunkirk, Clarebout Potatoes can process a combined total of 320 tons of potatoes per hour on its two production lines into frozen products in an endless variety of forms. It is not the largest site, but it is the most modern and efficient. For its construction, it called upon many of the contractors with whom it has good relations in Nieuwkerke and Waasten. Due to the size of the project, the piping was divided among seven contractors. “Each had their own zone to work in. We were responsible for the utility lines”, says Indinox Managing Director Emmanuel Martin.
Permanent team
Indinox started with a strong team and presence. On average, there were 30 to 35 people present on the site. Emmanuel: “In peak periods, that even rose to more than 50. It was impossible to handle it with just our own people. We did have a permanent team present that consisted of a project manager, a site manager and a number of regular welders and fitters. They formed the heart of the team and ensured the quality of the work delivered. They were supplemented by other team members, but also by subcontractors, steady partners we have known for years.”
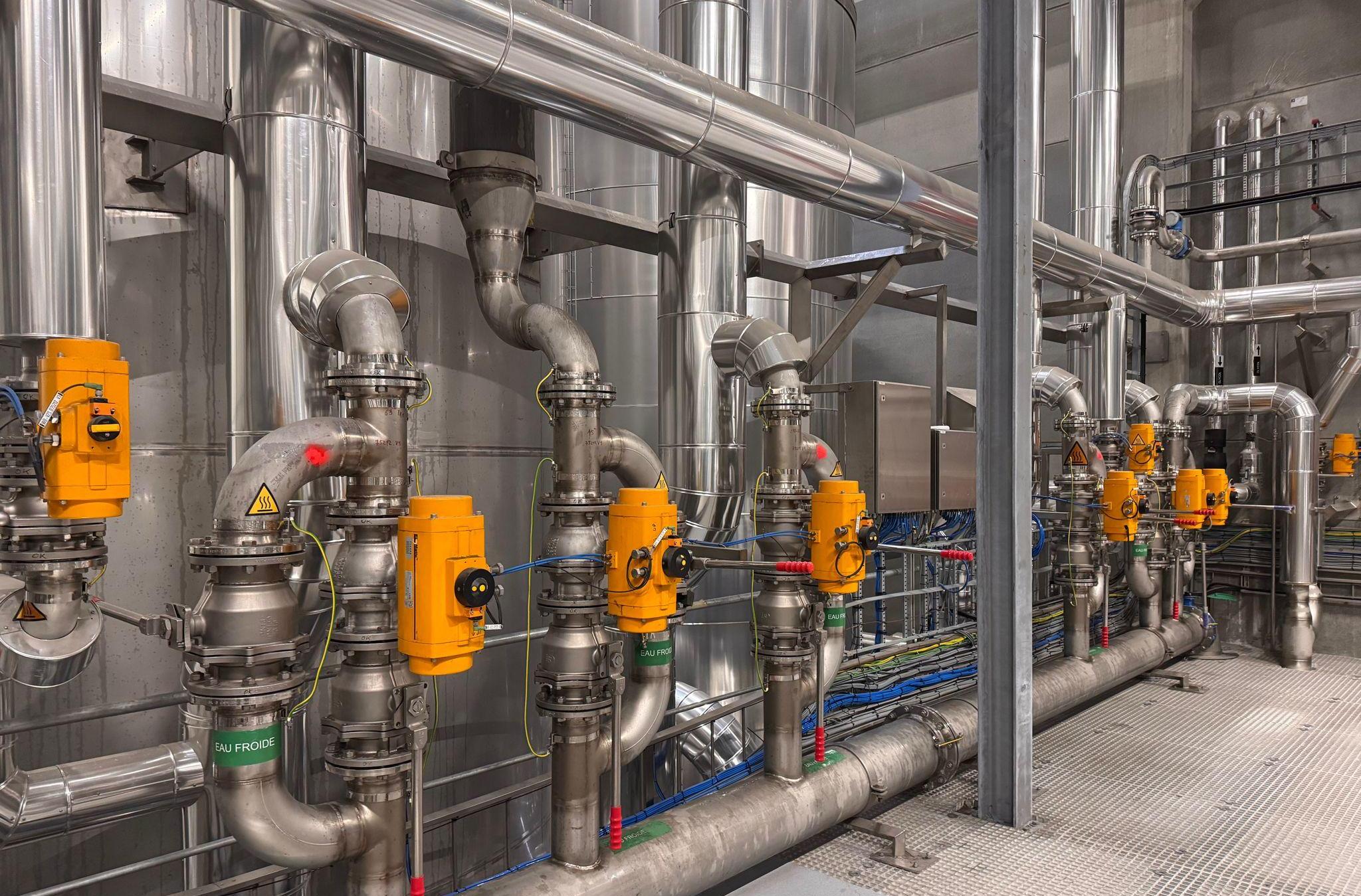
Safety first
They faced a tough challenge. A construction project of this size brings hundreds of contractors together on one site. This means that work has to be done efficiently, but above all safely. “This was not always easy, especially in the first phase. Our prevention advisor Stacy De Vuyst also visited the site a number of times to address safety issues. The local authorities eventually imposed restrictions to reduce the number of people allowed on site at any given time.” A setback? “Then you have to be able to switch gears quickly in planning, yes”, Emmanuel laughs. ”But that's exactly what we're good at. Because we have passionate employees who are willing to go the extra mile.”
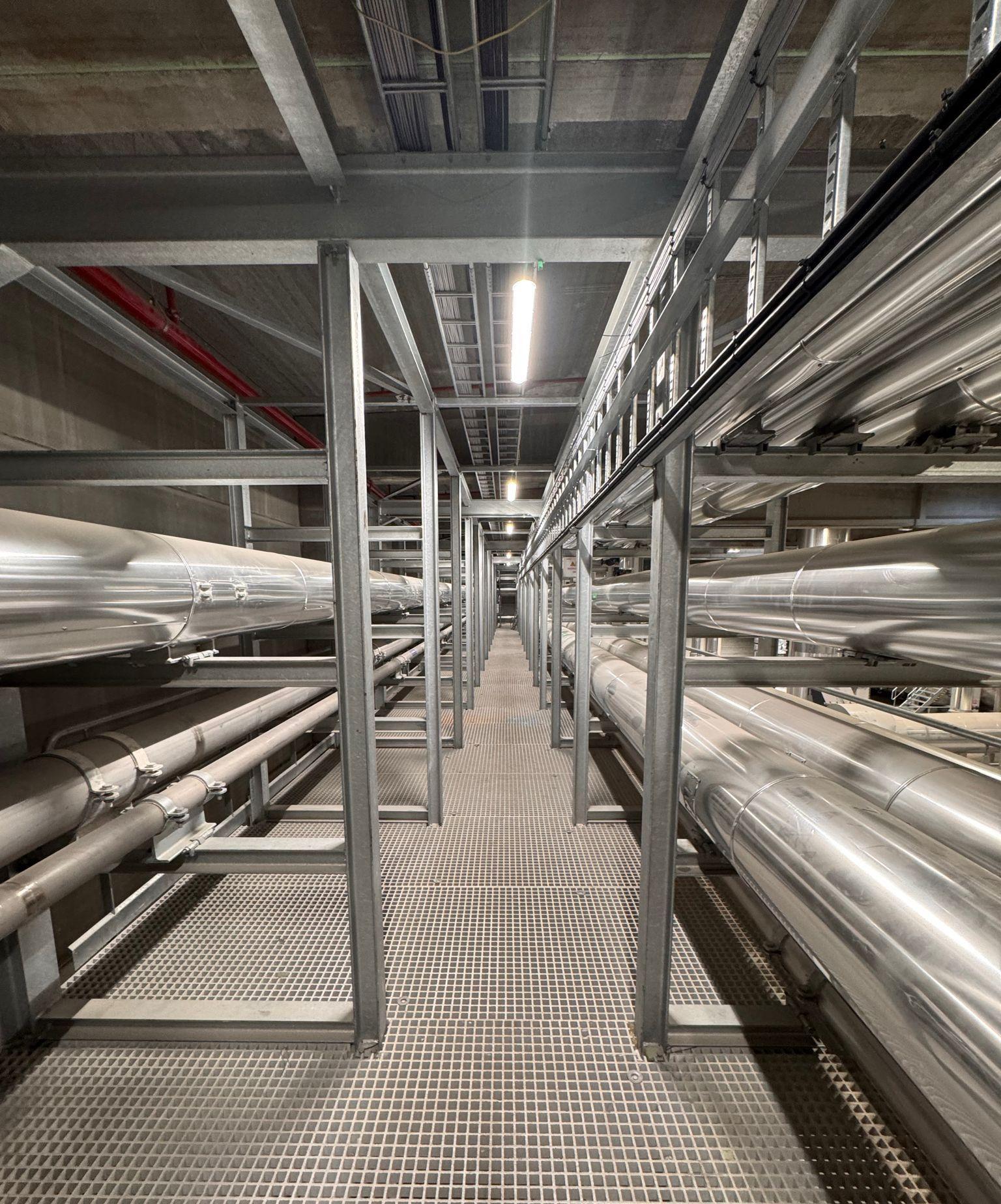
Imposed specifications
Clarebout Potatoes worked with imposed specifications for all the piping. There was nothing surprising in there for Indinox. “We already work closely with Clarebout in the other branches. We even provided our technical advice when drawing up the specifications there. So it's familiar territory”, explains Emmanuel. The fact that everything is made of stainless steel is self-evident in the food industry. Mostly in 316L stainless steel, some parts in 304. The diameters ranged from DN 15 to DN 300. “The oil pipes that get preheated with steam were jacketed piping”, adds Emmanuel.
Indinox France
Despite the challenging circumstances, Indinox succeeded in delivering the highest quality of piping of all the contractors. “That is what we want to stand for. Clarebout sets the bar very high in terms of quality, and so do we. Those who do not make the grade are not allowed to stay on board.” Indinox had also invested in a workshop in Dunkirk for this project. “Because we were able to prefab some of the compressed air lines. We made the isometrics for them ourselves. And it really made the difference on a site where so many people were working at the same time. We also see a lot of potential in this region, which is experiencing an industrial revival. We want to be and remain there and now we already have the perfect base for it”, concludes Emmanuel.
Let’s make your project flow
Need a reliable partner for your piping project? Indinox provides an efficient, hands-on comprehensive approach— from enquiry to execution and follow-up.